Fio retangular de alumínio/cobre coberto com filme de poliimida/poliéster
- Product Description:
- Features:
- Application:
- Properties:
- Perguntas frequentes
- embalagem e entrega
- Por favor, entre em contato conosco
Product Description:
Polyimide film sintering wire is made by copper or aluminum conductor. At first wrapped polyimide film which is coated with adhesive material on the conductor, and sintered film and film, film and conductor together.
The polyimide film wire is uniformly wrapped around the polyimide film or polyimide fluorine 4.6 composite film on the copper (aluminum) conductor. After heating, the fluorine 4.6 on the composite film is melted, so that the film and the conductor are bonded as a whole. This product has excellent voltage resistance, thin insulation thickness and heat resistance up to 220 ℃. It is mainly used for windings of motors, reactors, welding machines or other similar electrical products. The electrical bare copper (aluminum) wire produced by extrusion process is an ideal material for producing polyimide film clad wire.
Polyimide film is coated with a high temperature resistant binder and coated with a polyimide film strip. After heating, the thin film band becomes a continuous insulating layer. The winding wire has high temperature, low temperature and radiation resistance, the sealing, electrical and wear resistance. It is applied to steel rolling motor high temperature operation, traction motor, deep well pump motor and dry Transformer coil.
For Aromatic polyimide tape-covered aluminum magnet wire, after the aluminum magnet wire is taped with a tape that is 1.5 mm thick with 1.0 mm of this thickness being polyimide film and the remaining 0.5 mm being fluoroplastic, it is heated and heat-sealed.
Aromatic polyimide tape-covered aluminum magnet wire has a higher space factor than that of glass-fiber covered aluminum magnet wire and fully satisfy class-H heat resistance requirements. When Aromatic polyimide tape-covered aluminum magnet wire is used as substitute for these glass-fiber covered aluminum magnet wire, electrical equipment can be expected to be reduced in size and weight. Aromatic polyimide tape-covered aluminum magnet wire has electrical characteristics and coating flexibility far superior to those of glass-fiber covered aluminum magnet wire. Aromatic polyimide tape-covered aluminum magnet wire is primarily used for electric motors in vehicles, large direct current machines, and dry transformers. However, the aluminum magnet wire is more costly than other winding aluminum magnet wires. It is recommended, therefore, to use them when, there are problems in terms of space factor in particular. The aluminum magnet wire is inferior to glass-fiber covered aluminum magnet wire in corona resistance. When using the aluminum magnet wire in high-pressure equipment, special consideration must be given to insulation design.
Breakdown voltage of polyimide film covered copper/aluminum wire:
Método de encapsulamento | Insulation thickness mm | Tensão de ruptura ≥ | |
Nominal value | Tolerance | ||
Two layers polyimide self-locking wrapping | 0.15 | ±0.03 | 6000 |
Two layers of polyimide lap wrapped in opposite directions | 0.15 | ±0.03 | 6000 |
Three layers of polyimide lap wrapped in opposite directions | 0.23 | ±0.03 | 7000 |
Polyimide film aluminum wire is a multi-layer polyimide & fluoropolymer dispersion-coated film. The fluoropolymer coating functions as a heat-fusible layer for bonding to magnet wire conductors. It has superior scrape abrasion resistance and exhibits lower frictional properties than wire insulated with other commonly used polyimide materials. Polyimide film aluminum wire is ideal for demanding magnet wire applications and for difficult-to-wind motors.
Type:
- voltage resistant 4KV :double layer polyimide-fluoro 46 composite film wrapped copper flat wire
- voltage resistance 7.25kv :three-layer polyimide-fluoro46 composite film wrapped copper flat wire
- voltage resistance 8.7KV :three-layer polyimide-fluoro46 composite film wrapped copper flat wire
- voltage resistant 10KV :three-layer polyimide-fluoro46 composite film wrapped copper flat wire
Features:
Has high temperature resistance, Excellent mechanical and electrical properties, High moisture resistance and solvent resistance, Good formability, good mechanical strength, paint film adhesion, excellent electrical, scratch resistance, chemical resistance, thermal stability and solvent resistance;
Has good heat resistance, conditions in 180°C baking 24 hours performance unchanged;
High mechanical strength, good abrasion resistance and flexible;
Excellent withstand voltage properties;
Resistant to moisture absorption, moisture proof;
High breakdown voltage up to 5000~10000V (as required);
Compared to glass-fiber wound wire, lightweight specific gravity, thus reducing purchase cost;
Application:
Application: rectifier, reactors winding, coil for electronic communication lighting, sealed submersible motor, micro generator, heat resistant Transformer, contactor, solenoid valve.
Copper wire: suitable for traction motor, submersible motor, salt field motor, lifting motor and other high voltage motor . It is high temperature, cold-resistant, anti-radiation, anti-burning, resistant to organic solvent.
Aluminum wire: suitable for high voltage, high power, high temperature, high humidity environment.
Product breakdown voltage should follow below table(Non woven fabric / polyester film wrapping):
Wrapping type | Insulation Thickness(mm) | Breakdown voltage above | |
Standard Value | Tolerance | ||
2 layers of polyester films | 0.22 | ±0.03 | 5000 |
2 layers of polyester films+1 layer of non-woven fabrics | 0.33 | ±0.03 | 5000 |
3 layers of polyester films | 0.3 | ±0.03 | 7500 |
3 layers of polyesters film+ non-woven fabrics | 0.42 | ±0.03 | 7500 |
This product is made of oxygen free Aluminum/Copper rod or electrical round aluminum/Copper rod through a certain specification of the die extrusion or drawing after annealing treatment of the wire, and then on the Aluminum/Copper magnet wire strips on the 2-3 layer of polyester film or Non-woven Fabrics electrical insulation layer of the winding wire, the product is good, temperature resistance and other grade 130for B grade, mainly used for air core reactor.
Properties:
Properties:
Property items | Unit | Typical value | |||||||
25μm | 40μm | 50μm | 75μm | 100μm | |||||
Density | g/cm3 | 1420±20 | |||||||
Tensile strength | Longitudinal | Mpa | ≥135 | ||||||
Horizontal | ≥115 | ||||||||
Elongation | Longitudinal | % | ≥30 | ||||||
Horizontal | ≥35 | ||||||||
Dielectric strength | Average Value | Mv/m | ≥150 | ≥130 | ≥110 | ||||
Single value | ≥100 | ≥80 | ≥70 | ||||||
Surface resistivity 200℃ | Ω | ≥1.0X1013 | |||||||
Volume resistivity,200℃ | Ω.m | ≥1.0X1010 | |||||||
Dielectric constant,48~62Hz | ____ | 3.5±0.4 | |||||||
Media dissipation factor,48~62Hz | ____ | ≤4.0X10-3 | |||||||
Temperature for long term heat-resistance | ____ | ≥180 | |||||||
Sizes:
1). Thickness and tolerance
typical thickness | 25um | 30um | 50um | 75um | 100um |
Thickness tolerance: | +4 | +6 | +7 | +8 | +10 |
-3 | -5 | -6 | -6 | -7 |
2). Width: 0 – 700mm and also can be cut to the sizes according to customer’s requirement.
3). Length: As customer’s demand.
Test Report (2.12*7.10 mm):
Product name: Polyimide covered flat copper wire(imide) | ||||
Type: SBEMB-30/180 | Test No.: 20210629 | |||
Specification: 2.12*7.10 mm | Technique standard: GB/T7673.3-08 | |||
Test subject | Technical requirement | Test result | ||
Appearance | Tightness, uniformity, smooth | Qualified | ||
Size | a side | 2.12mm+0.03mm | 2.10mm | |
b side | 7.10mm+0.07mm | 7.11mm | ||
Radius | 0.65mm±25% | Qualified | ||
Film thickness | 0.24 -0.33mm | 0.29 mm | ||
Maximum A side size | 2.48 mm | 2.39mm | ||
Resistivity | 20℃≤0.017241Ω. mm²/m | 0.017190Ω. mm²/m | ||
Elongation | ≥ 32 % | 40% | ||
Spring back | ≤5.5 degree | 4.0 degree | ||
Flexibility adhesiveness | Bending | No crack, no rip | Qualified | |
Adhesiveness(cutting) | No lose adhesiveness after stretching 10% | Qualified | ||
Work temperature | 260-300 | Qualified | ||
Breakdown Voltage | ≥ 2.5 KV | 3.2 3.4 3.5 3.2KV | ||
Appraisal result | Qualified | |||
Perguntas frequentes
[Q]: What’s your mainly products?
A : Our mainly products are :
Polyimide/ Polyester Film Magnet Aluminum/Copper wire /Rectangular Enameled wire/ Round Enameled wire/Ultra Fine Rectangular Enameled wire/NOMEX paper wrapped wire/ Kraft paper wrapped wire/ carton covered wire/Fiber glass wrapped enameled wire/ Electrical rectangular wire/Macromolecule enameled wire, etc.
Our CERTIFICATE AND STANDARD:
- Manufacture standard: IEC Standard
- ISO9001:2000 Quality Management System
- Enameled Copper Clad Aluminum wire (ECCA): ROHS Authentication
- Enameled wire (ECCA ,ECU ,EAL):SGS Authentication
[Q]: How about your company’s annual production capacity?
A : Our Company’s annual production is about 8,000 tons.
[Q]:What’s your company ‘s product scope?
A : We have many kinds of products ,such as enameled aluminum wire, enameled cooper wire, paper covered magnet wire, fiber glass covered magnet wire and other aluminum/cooper magnet wire products.
[Q]: What’s the temperature-resist grade of your Polyimide Film Magnet Wire?
A : We produce the thermal class of enameled aluminum wire from 130 to 220 Centigrade.
[Q]: What is specifications of Polyimide Film Magnet Aluminum/Copper wire your company can produce?
A : Film covered round (Al & Cu) wire: 1.00mm-8.00mm
Film covered rectangular AL wire: Side (a): 0.90mm-8.00mm Side(b): 2.00mm-25.00mm
Film covered rectangular Copper wire: Side (a): 0.90mm-5.60mm Side(b): 2.00mm-22.00mm
[Q]: Could you provide the free samples?
A : Yes, We are honored to offer you samples, We could provide the free samples within 0.5kg. You only need undertake the express charges.
[Q]: What’s the price of your enameled aluminum wire?
A : Please sent an email to our email https://enamelled-wire.cn or WhatsApp: 86-13752439076, our salesman will reply you as soon as possible.
embalagem e entrega
Packaging Details:
Inner packing: in different wooden spool, such as 30/50/150kg wooden spool, or according to your wire diameters
Standard packaging: 30kg ~150kg ply-wood spool (250*400 /250*500/ 250*600 / 250*730)
Outer packing: wooden spool and wooden case or according customers’ special requirement
Port: Qingdao, Shanghai, Tianjin
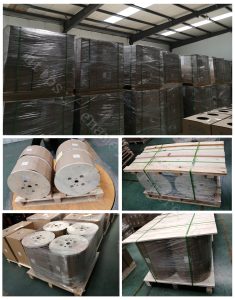
Por favor, entre em contato conosco
Senhorita: Lídia
Mob: 86-13752439076 Fax: 86-22-60863016
WeChat: 86-13752439076 WhatsApp: 86-13752439076